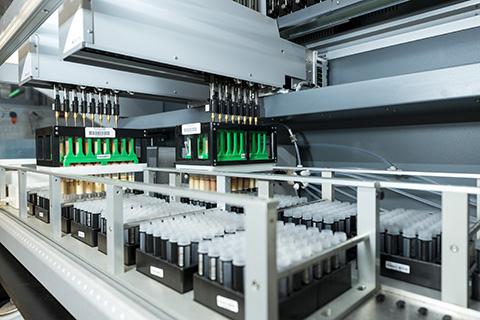
The Natural Products Branch’s version 1 labware running during methods development. “The green racks are 3D printed to accommodate the additional adapter we needed to make the Tecan [instrument] do what we wanted. Changing those required that we change the shuttle superstructure (black above the green, also 3D printed) that holds the racks and columns tight against the shuttle (white milled polypropylene riding on the aluminum rails),” Harris wrote in a message. (Photo from the SPGM archive)
In the Natural Products Branch, projects demand a level of precision that makes Cinderella’s slipper look like child’s play. However, lab equipment isn’t always tailor-made for such uniqueness, sometimes requiring a little modification with special parts to get the job done. Sometimes those parts aren’t available.
It rightly sounds like a headache, but Jason Evans and Matthew Harris say the group regularly pulls it off—at times, even in as little as a day.
That’s all thanks to ingenuity coupled with 3D printers in their lab.
“We’ve managed to solve a lot of problems and improve our throughput way beyond where it would have been without the 3D printing,” said Harris, a Frederick National Laboratory research associate supporting the group.
Less Hassle, Less Expense
The Natural Products Branch recovers, extracts, and screens potential medicinal compounds from naturally occurring sources like plants, fungi, and marine invertebrates. Few groups in the world do it on the scale they do—where some projects encompass several thousand samples—and fewer still have solutions for when the technology doesn’t fit.
That means most solutions must come from within.
For instance, the team once encountered challenges with a liquid handler designed for a major project with very specific labware requirements. They discovered the work needed higher pressures than the liquid handler could deliver. Harris and Evans found a solution but realized that a significant portion of the labware needed to be redesigned to accommodate the necessary changes. The 3D printers let them make it happen.
It sounds small, but when machines in a high-volume, high-precision lab don’t work, research becomes jeopardized.
External solutions, when they exist, are often less than ideal. During one project, a vendor offered to make the necessary parts for $15,000. In another, an equipment manufacturer stocked the right part—special jaws that allowed an automated workstation to unscrew vial caps—but just one would’ve cost tens of thousands of dollars.
And if a part’s dimensions are off by even a millimeter, it may not work and may need to be re-engineered, Harris said. That becomes costly and impractical when working with a vendor.
Instead, Harris usually fires up his engineering software and creates his own designs. Sometimes they need to be refined, but thanks to 3D printing’s accessibility, the hassle is manageable and the cost is pocket change compared to buying externally.
Benefits Beyond the Bottom Line
The group owns two printers. One uses a method called fused deposition modeling (FDM), in which a nozzle deposits layers of heated plastics that fuse together to create the final object. The other uses stereolithography (SLA), a technique where a laser cures the outline of the part in a vat of liquid plastic, hardening portions of it into the final shape. The versatility lets the group easily address different machines’ shortcomings.
“I would also make an argument that it helped improve morale in the group,” said Evans, the group’s scientific programmer. 3D-printed solutions, such as special prongs Harris designed for a vial-handling device, have allowed the lab staff to automate equipment to the point it can be left unattended. That saved them frustration and freed them up for other pressing tasks, Evans said.
Some staff have also learned to recognize opportunities for modifying lab equipment via 3D printing, and Harris says they’ll often plan ahead for it when purchasing new devices. It has made life in the lab easier.
‘I Can Solve Any Problem’
Things have come far since the group started 3D printing as a pilot project eight years ago. Back then, John Britt, a Frederick National Laboratory senior programmer analyst supporting the group, suggested purchasing a printer to try to address some technological gaps in the face of process challenges and tight schedules. The plan was to print prototype parts and have a machinist make a refined version, but “it turns out what we were printing, generally, was just fine,” Evans said.
For a $1,500 investment for their first printer—practically a steal in the world of commercial lab equipment—the group equipped itself to overcome major limitations.
“It solves a lot of problems, and then it turns into, ‘I can solve any problem. We can 3D print a solution to that,’” Evans said.
They aren’t alone, either. The National Institutes of Health has a 3D printing user group that shares designs and best practices. There are also multiple websites where labs can upload their designs for others to download.
Harris says it “democratizes the solution” because anyone with a printer can make the equipment if they download the design. While that benefits budget-conscious groups like the Natural Products Branch, it’s an even bigger boost to labs in resource-limited areas where purchasing new parts or equipment isn’t feasible.
It’s a special form of scientific collaboration, as important to the spirit of science as collaborating on a study.
“The collaborative effort on that sort of thing is so much faster and so much more achievable for a variety of different groups,” Harris said.
Samuel Lopez leads the editorial team in Scientific Publications, Graphics & Media (SPGM). He writes for newsletters; informally serves as an institutional historian; and edits scientific manuscripts, corporate documents, and sundry other written media. SPGM is the creative services department and hub for editing, illustration, graphic design, formatting, multimedia, and training in these areas.
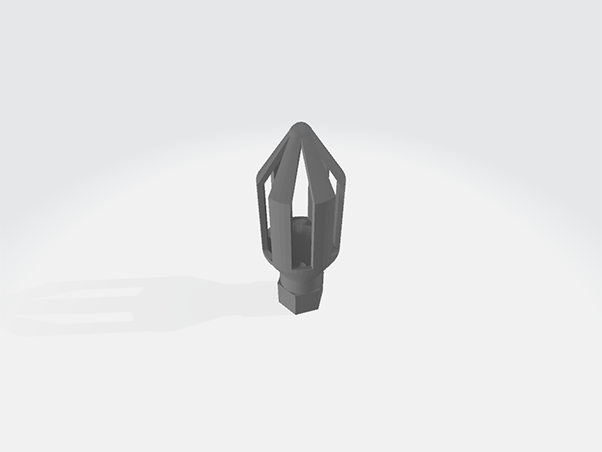
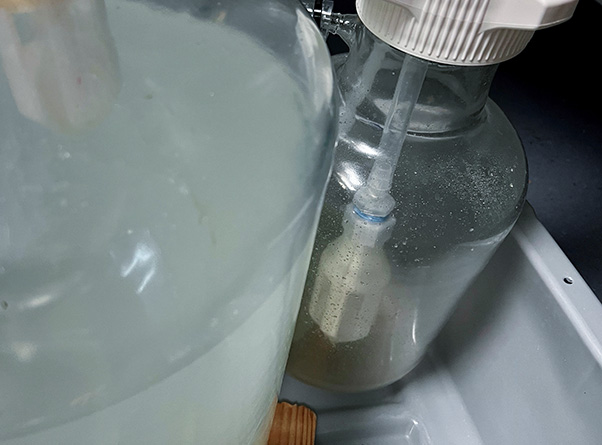
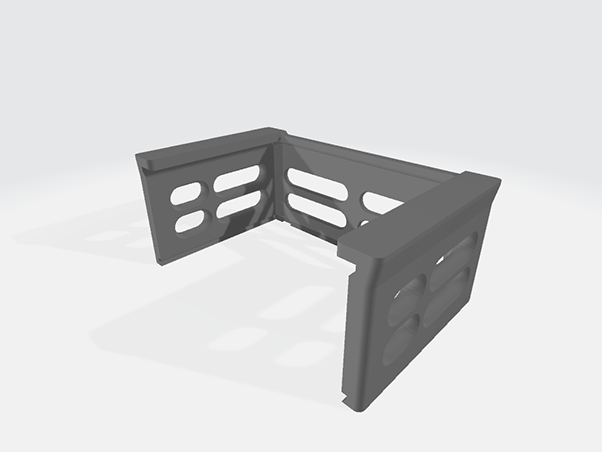
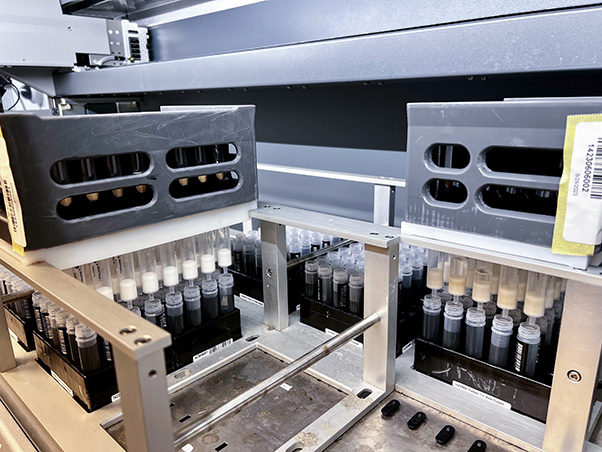